Thanks Caddman.
I like to use the lathe to single point cut the threads whenever possible. It is a lot more precise than I could ever accomplish doing it all by hand with a die wrench. And for a project like this, you want as much precision fitting as humanly possible.
I won't pretend that my tool or handiwork is as accurate as a CNC machine, but I can guarantee that it's better than anyone could do by hand. And with as close tolerances as I'll need for it in the end, I want the best I can do.
The bed on my lathe is dated 1986. It was barely used at all when I bought it from my friend. It was his late Fathers. He probably hadn't used it maybe 3 times. His cutter bits didn't even hardly show any wear at all on them.
I was able to score a Bushnell Sportsman 1.5-4.5 optic with a circle x reticle that I like on ebay for $40 shipped. I couldn't pass it up. For the way that I use the gun and how I hunt, the low power optics work the best for me.
The scope was already camo'd in Realtree AP, and while that is slightly different pattern than what I have on the receiver, and even a slightly different pattern than what is on the stock too, it all will blend together well.
The main difference in the scope pattern, it has some "pine tree needles" artwork, while my other patterns do not have pine needles. And ironically and probably luckily for me, the rings will cover the majority of the pine needle artwork and it still has some green leaves.
Here's the scope as I took it out of the box, along with a ring that I camo dipped this morning with the realtree pattern I had. The other ring was still a little tacky and why it wasn't in the picture but it is essentially the same as this one.
I like to use the lathe to single point cut the threads whenever possible. It is a lot more precise than I could ever accomplish doing it all by hand with a die wrench. And for a project like this, you want as much precision fitting as humanly possible.
I won't pretend that my tool or handiwork is as accurate as a CNC machine, but I can guarantee that it's better than anyone could do by hand. And with as close tolerances as I'll need for it in the end, I want the best I can do.
The bed on my lathe is dated 1986. It was barely used at all when I bought it from my friend. It was his late Fathers. He probably hadn't used it maybe 3 times. His cutter bits didn't even hardly show any wear at all on them.
I was able to score a Bushnell Sportsman 1.5-4.5 optic with a circle x reticle that I like on ebay for $40 shipped. I couldn't pass it up. For the way that I use the gun and how I hunt, the low power optics work the best for me.
The scope was already camo'd in Realtree AP, and while that is slightly different pattern than what I have on the receiver, and even a slightly different pattern than what is on the stock too, it all will blend together well.
The main difference in the scope pattern, it has some "pine tree needles" artwork, while my other patterns do not have pine needles. And ironically and probably luckily for me, the rings will cover the majority of the pine needle artwork and it still has some green leaves.
Here's the scope as I took it out of the box, along with a ring that I camo dipped this morning with the realtree pattern I had. The other ring was still a little tacky and why it wasn't in the picture but it is essentially the same as this one.
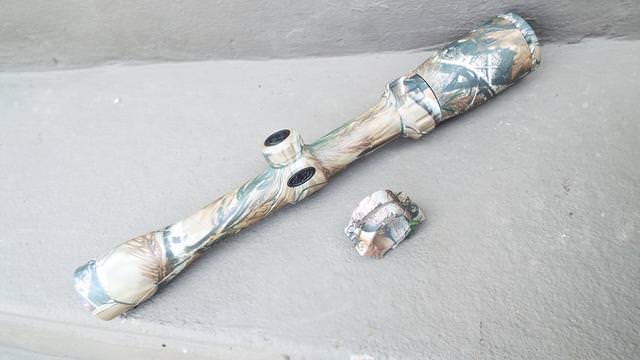
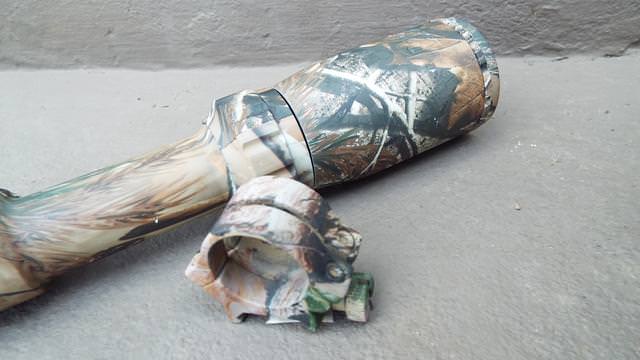